Search
Mining industry
Achievements
- home
- achievements
- mining industry
- refurbishing of a gyratory crusher shaft
Refurbishing of a gyratory crusher shaft
Our client : A major Quebec mining company
A complex project in so many ways
To refurbish a gyratory crusher shaft and its sleeve, our client absolutely had to do business with a company that could deal with the parts’ oversized proportions.
Assembling the shaft and sleeve, which weigh over 55 tons and measure nearly 7 meters high, had every characteristic of a headache, even for the best equipped of companies!
And the challenges didn’t stop there: the hardness of the metal used to crush ore and the shaft and sleeve’s cone shape brought other requirements to be considered.
Fortunately, FAB 3R’s facilities have unusual—nearly unique—capacities in North America for huge jobs. This, and our experience with unusual and complex projects, made us the perfect partner for the job.
Parts handled with power and skill
To refurbish the assembly, FAB 3R faced a series of tricky tasks: disassembling it, removing deposits from wear and debris, adding new materials, ensuring stress release, machining the shaft and sleeve, carrying out various tests (including a methylene blue test) and finally reassembling it.
But before all that? We first had to successfully bring the assembly to the pit where it could be taken apart. To do this, enough space had to be freed up for the crane carrying the assembly, and it had to get through without disrupting other projects underway. Talk about logistics!
To be reconditioned, the parts first had to be taken apart. Given the height required to remove the sleeve and shaft (a minimum of the combined height of the two), FAB 3R didn’t have a choice: the assembly had to be placed vertically in a pit. The team also had to make sure the parts would be stable enough throughout the disassembly to support the 500 tonnes of pressure exerted by the hydraulic cylinder! Our specialist did some out-of-the-box thinking to set all the required tooling to secure the parts.
Machining the sleeve was also an unusual challenge. Given its cone shape, it wasn’t a possibility to use a traditional steady rest, which wouldn’t have provided uniform support. Instead, we had to design customized tooling that would stabilize it according to the axes of the machine and keep it perfectly balanced during the machining.
Just the disassembly and reassembly required strength and the appropriate facilities, but to conduct the methylene blue test, FAB 3R also had to show off a little of its fancy footing. We had to delicately insert the pieces one into the next, aligning them with surgery-like precision in their final positions. Any rubbing would have falsified the test results!
When skill overcomes difficulty
At the end of the day, FAB 3R’s experience, creativity, organization and fine-tuned skill—in addition to having facilities perfect for this kind of job—allowed us to overcome the obstacles and deliver the parts right on schedule, as planned.
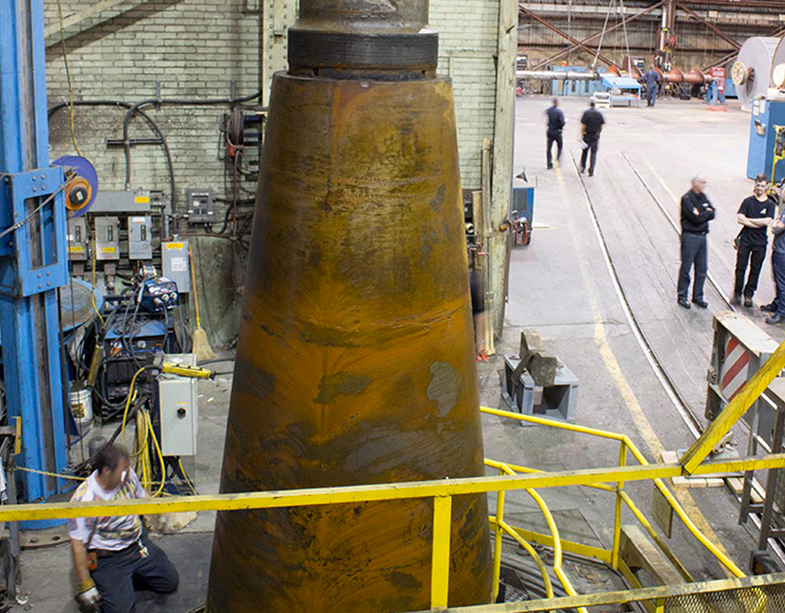
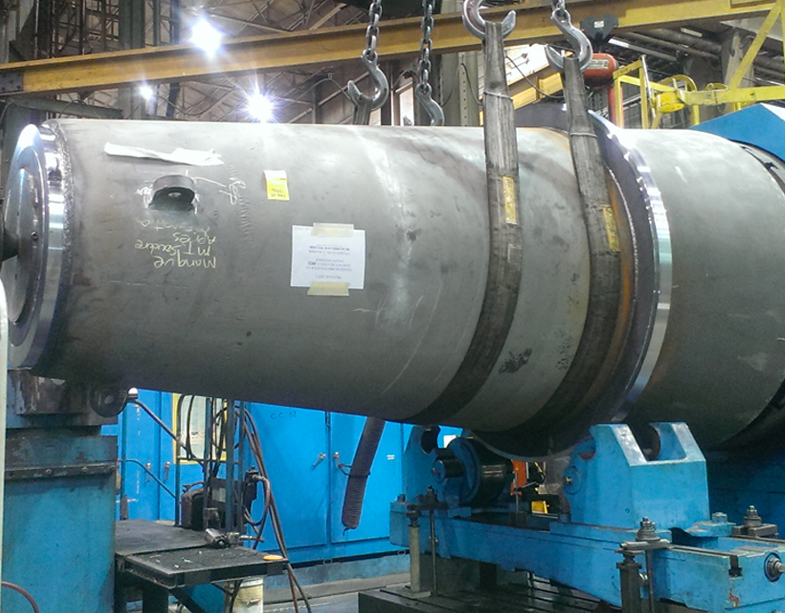
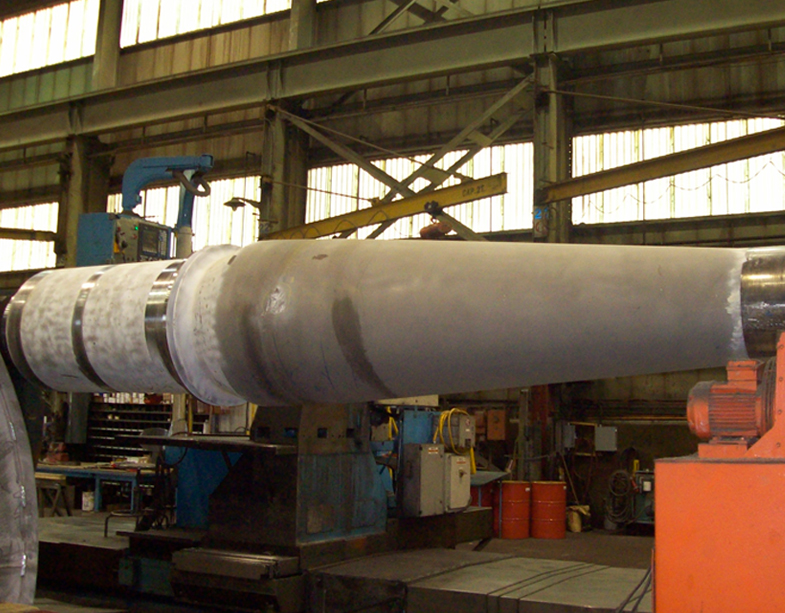